Introduction
Hello, I’m excited to share my insights with you. I work with IceStar Energy Technology Co., Ltd, where we have over 20 years of experience in designing, manufacturing, and delivering industrial cooling and heat exchange solutions. In my work, I have seen firsthand how air-cooled chillers can solve many cooling challenges across various industries. I write this article to help you understand the different types, applications, and principles behind air-cooled chillers, and to share ideas that may guide your next investment in cooling technology.
Air-cooled chillers are essential for efficient cooling in many industrial and commercial applications. With types including scroll, screw, centrifugal, portable, and modular, these systems work on the simple yet effective principle of heat exchange. Their key components—such as the evaporator, compressor, condenser, expansion valve, and controls—ensure optimal performance, energy efficiency, and reliability. This article breaks down these elements, highlights real-world applications, and compares air-cooled chillers to water-cooled systems to help you make an informed decision.
Many companies face problems when it comes to choosing a cooling solution that is both efficient and cost-effective. I understand your frustration with rising energy costs, complex installations, and maintenance issues. That is why I want to share with you the benefits of air-cooled chillers, discuss their many types and applications, and explain the underlying principles in a simple way. As we explore this topic together, you will discover how these chillers can address your challenges and support your business needs.

Types, Applications, and Principles of Air Cooled Chillers
Exploring the Types of Air-Cooled Chillers
When it comes to cooling solutions, I have seen many businesses benefit from using air-cooled chillers. These chillers come in several types, each tailored to meet different operational needs. For instance, scroll chillers are known for their smooth and efficient operation, while screw chillers are favored for their reliability in heavy-duty applications. Centrifugal chillers are widely used in large commercial buildings because they offer high efficiency. Additionally, portable air-cooled chillers provide flexibility when temporary cooling is needed, and modular chillers are designed to fit a variety of cooling requirements with different compressor types.
Below is a table that outlines the key types of air-cooled chillers, their main features, and typical applications:
Type | Description | Typical Applications |
Scroll Chillers | Use scroll compressors for smooth, efficient cooling. | Commercial cooling, small industrial processes |
Screw Chillers | Employ screw compressors for reliable performance in continuous operations. | Heavy industrial processes, manufacturing plants |
Centrifugal Chillers | Use a rotating centrifugal pump to compress refrigerants for high capacity. | Large commercial buildings, industrial processes |
Portable Air-Cooled Chillers | Designed for temporary or supplemental cooling needs. | Emergency cooling, temporary installations |
Modular Chillers | Offer various compressor options including centrifugal, screw, or scroll. | Flexible industrial and commercial installations |
This table not only helps you see the differences at a glance but also aids in understanding which chiller might best suit your needs. For more detailed technical insights, I recommend exploring the ASHRAE website which offers extensive resources on HVAC systems and components.
Understanding the Applications
Air-cooled chillers are versatile and serve a wide range of industries. They support industrial processes, commercial cooling, equipment protection, and even specialized environments like medical and military facilities. In industrial settings, these chillers help maintain optimal temperatures for machinery and products, while in commercial spaces, they provide reliable air conditioning. Their ability to work without the need for water infrastructure makes them ideal for remote or water-sensitive areas.
I have seen many companies successfully integrate air-cooled chillers into their operations. In the industrial sector, these chillers maintain the required temperature for processes in plastics, pharmaceuticals, and food processing. They extract excess heat from equipment, stabilizing the environment and protecting sensitive machinery. In commercial settings, air-cooled chillers are used in offices, shopping malls, and hotels. Moreover, they play a critical role in cooling electronic equipment in data centers and protecting delicate systems in medical facilities.
Let’s break down the applications further:
– Industrial Processes: They regulate temperatures in automotive manufacturing, chemical processing, oil and gas refineries, and printing facilities.
– Commercial Cooling: They are effective in cooling offices, shopping malls, and large public buildings.
– Equipment Cooling: They safeguard servers and critical electronic systems.
– Medical and Pharmaceutical: They ensure the safe operation of clean rooms, storage areas, and production areas.
– Military: They efficiently cool living quarters and electronic systems in challenging environments.
For a deeper dive into industrial cooling applications, you may find this article on the U.S. Department of Energy website very useful.

Unpacking the Principles Behind Air-Cooled Chillers
Air-cooled chillers work on a simple yet effective principle: heat exchange. The process starts when a hot liquid refrigerant flows through coils in the condenser. A fan blows air over these coils, absorbing heat from the refrigerant. This causes the refrigerant to condense into a liquid. The cooled liquid is then circulated to remove heat from various sources.
Here are the key components that I have seen consistently drive the operation of air-cooled chillers:
Evaporator: Absorbs heat from the process water or fluid that needs cooling.
Compressor: Increases the pressure and temperature of the refrigerant vapor.
Condenser: Rejects heat from the refrigerant, turning it back into a liquid.
Expansion Valve: Reduces the refrigerant pressure, cooling it further.
Controls: Monitor and adjust the process for optimal performance.
The refrigeration cycle can be summarized as follows:
1. The compressor raises the temperature and pressure of the refrigerant gas.
2. The condenser removes the heat using ambient air, turning the gas into a liquid.
3. The expansion valve reduces the refrigerant pressure, resulting in further cooling.
4. The evaporator absorbs heat from the water, producing chilled water to be circulated.
This cycle is repeated continuously to provide steady cooling. I appreciate how this process not only keeps systems cool but also improves energy efficiency. For more detailed explanations, you might want to review technical resources on Energy.gov which explain the refrigeration cycle in depth.
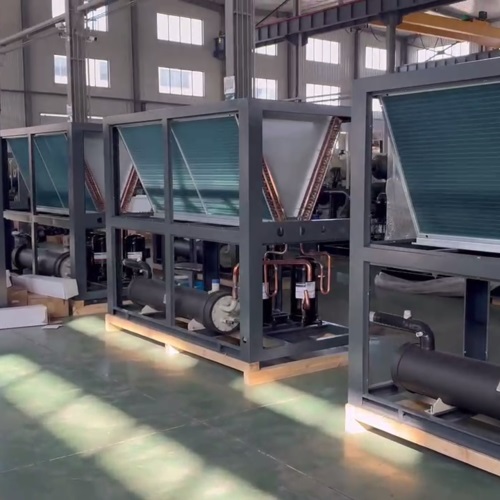
Advantages of Air-Cooled Chillers and Comparison with Water-Cooled Chillers
What are the Advantages of Air-Cooled Chillers?
As I work with various cooling systems, I have come to value the numerous advantages of air-cooled chillers. They are particularly popular because they simplify installation and maintenance. Many businesses appreciate that these systems do not need a separate water infrastructure. This saves both time and money in installation. Additionally, air-cooled chillers are known for their reliability and lower operating costs.
Air-cooled chillers offer significant advantages such as cost savings, energy efficiency, and flexibility. They require less space and do not depend on water, which makes them ideal for areas with limited water resources. Their design minimizes maintenance requirements and reduces operating costs, making them a practical choice for many industries.
When I compare these chillers to traditional water-cooled systems, I notice several clear benefits. First, the absence of water towers, pumps, and extensive piping means lower upfront costs. Second, the lack of water eliminates issues like scaling, corrosion, and the need for chemical water treatment. Finally, their compact design means they can be installed in areas with space constraints, such as rooftops in urban environments.
For additional context on the benefits of air-cooled systems, I suggest visiting HPAC Magazine where experts regularly discuss the cost and energy advantages of these systems.
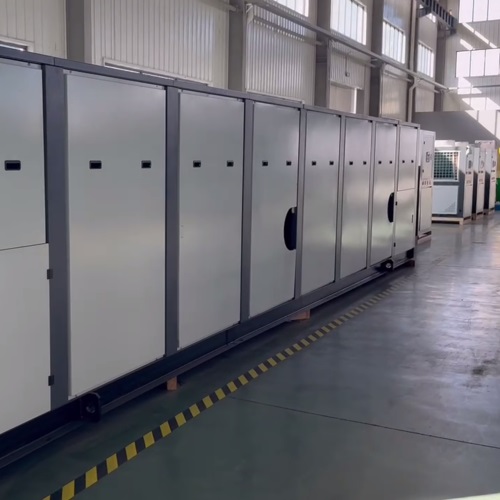
Which is Better: Air-Cooled or Water-Cooled Chillers?
The choice between air-cooled and water-cooled chillers depends on your specific needs and circumstances. In my experience, each system has its merits, and the best option varies with the application. Air-cooled chillers have lower installation costs, simpler maintenance, and are more robust in cold weather conditions. They are especially advantageous in regions where water is scarce or expensive.
Air-cooled chillers are often better for installations with limited space and water resources. They are less complex to install and maintain, which can lead to long-term savings. On the other hand, water-cooled chillers may offer higher energy efficiency for large-scale applications, but they require additional infrastructure and ongoing water treatment.
In my work, I have seen water-cooled chillers perform well in large facilities where the cooling load is immense and a stable water supply is available. They are typically installed indoors, which protects them from harsh weather and helps maintain quieter operations. However, the higher maintenance and installation costs can be a drawback for many businesses. Ultimately, the decision should be based on factors such as your facility’s size, available space, climate, and water availability.
For a comprehensive comparison of the two systems, you might want to explore resources like the U.S. Department of Energy’s HVAC information, which provides detailed performance analyses and cost comparisons.
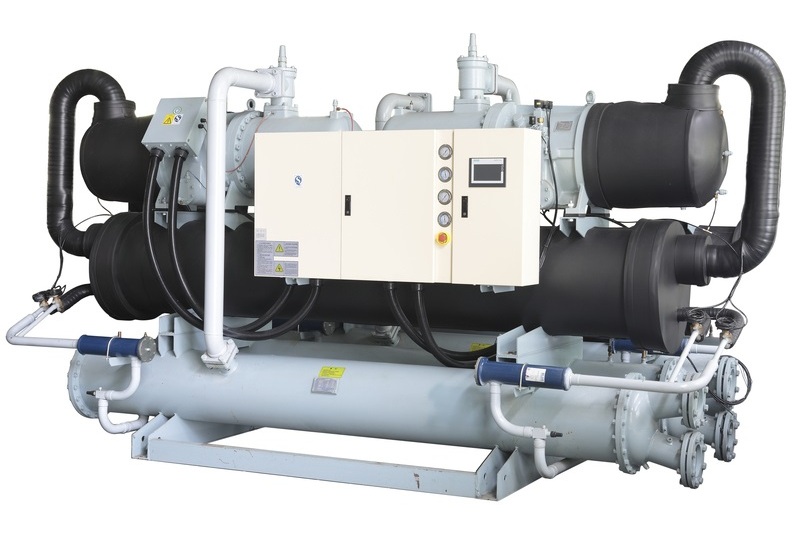
Further Explanation and Insights
I believe it is important to summarize the key insights that I have learned over the years. Air-cooled chillers are a practical solution that meets many cooling challenges. Their simplicity in design leads to lower installation and maintenance costs, which can significantly benefit your operations. They are especially useful in regions with water limitations, as they operate solely on ambient air to dissipate heat.
In contrast, while water-cooled chillers may offer greater energy efficiency in certain scenarios, they also bring added complexity. The need for water treatment, additional equipment, and maintenance can increase long-term costs. I have observed that companies with limited installation space or those in drought-prone areas often find air-cooled chillers to be a superior choice. This insight is supported by several industry experts who emphasize the advantages of reduced water consumption and ease of installation.
Moreover, air-cooled chillers have proven their reliability in harsh weather conditions. They continue to perform efficiently even when temperatures drop below freezing. This characteristic makes them a versatile choice in both urban and remote locations. It is clear that when you weigh the benefits of lower operational costs and flexible installation, air-cooled chillers stand out as an excellent option for many applications.
Conclusion
In this article, I have shared my personal insights and expertise on the types, applications, and principles of air-cooled chillers. We explored how scroll, screw, centrifugal, portable, and modular chillers work, and discussed their use in industrial, commercial, and specialized settings. I also explained the basic principles of the refrigeration cycle and the roles of key components like the evaporator, compressor, condenser, and expansion valve.
Furthermore, we examined the significant advantages of air-cooled chillers, including cost savings, energy efficiency, and ease of installation. I compared these benefits with the attributes of water-cooled chillers, highlighting that the best choice depends on your unique circumstances, such as available space, climate, and water resources.
I hope this article has provided you with clear and actionable information that will help you make better decisions for your cooling needs. At IceStar Energy Technology Co., Ltd, we are proud to offer customized industrial cooling and heat exchange solutions backed by over 20 years of expertise. If you have any questions or need further advice, please do not hesitate to reach out. Your success in achieving efficient and reliable cooling is our top priority.
For further reading and detailed technical insights, please visit reputable resources such as:
ASHRAE Technical Resources
U.S. Department of Energy – Buildings
HPAC Magazine – Chiller Systems
Thank you for taking the time to read this article. I look forward to helping you achieve optimal cooling solutions that drive efficiency and support your business growth.