I have been working in the industrial cooling field for many years. I have seen many changes in the way we manage temperature control. I understand that you, like me, care about reliable and efficient cooling systems.
I know you are looking for answers. You need a simple, clear explanation of air-cooled chillers and their operations. In this article, I share my insights and practical experiences to help you understand these systems. I will discuss their basic principles, common errors, repair tips, and retrofitting ideas in a friendly, personal way.
In this article, I will take you step by step through the world of air-cooled chillers. I will explain what they are, how they work, and why they are so important for industrial applications. Together, we will explore useful tables and external links to enrich our discussion. Let’s dive in and explore this vital technology that powers efficient cooling systems.
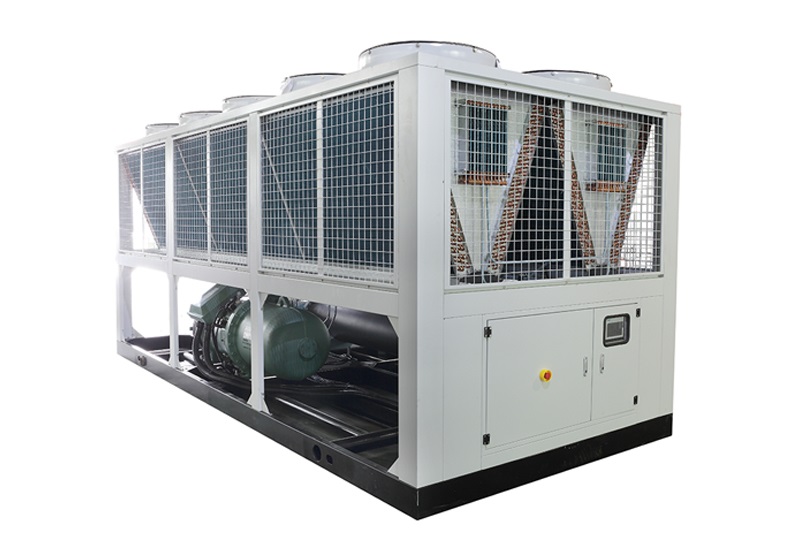
What Are Air Cooled Chillers and How Do They Work?
I have always been fascinated by the simplicity and effectiveness of air-cooled chillers. These systems are key in many industrial and commercial facilities. They work by using the ambient air to reject heat. I learned that this technology is based on the principles of thermodynamics. In an air-cooled chiller, the refrigerant absorbs heat from a liquid or air stream. Then, the system releases that heat into the environment. This process is efficient and very practical in many settings. You might have seen these systems in office buildings, hotels, and data centers.
Air-cooled chillers operate using a closed-loop refrigeration cycle. They extract heat from a process medium and reject it using fans that blow ambient air over condenser coils. This design eliminates the need for cooling towers and extra water infrastructure.
Let me break down the process for you. The core function of an air-cooled chiller is to remove heat from a target medium. This medium is usually water or a water-glycol mix. The process involves four key stages: evaporation, compression, condensation, and expansion. The refrigerant absorbs heat during the evaporation stage. Then, it is compressed, which raises its temperature. In the condensation stage, fans blow air over the condenser coils. This causes the refrigerant to condense into a liquid. Finally, the expansion valve reduces the refrigerant’s pressure and temperature before it returns to the evaporator.
To help you visualize these components, please see the table below:
Component | Function |
Evaporator | Absorbs heat from the process medium (water or water-glycol mixture). |
Compressor | Increases the refrigerant’s pressure and temperature. |
Condenser | Uses ambient air and fans to cool and condense the refrigerant. |
Expansion Valve | Lowers the refrigerant’s pressure, cooling it before it re-enters the evaporator. |
For more detailed background, you can visit Wikipedia on Refrigeration and Wikipedia on Chillers.
Which are the Common Errors in Air-Cooled Chillers?
I have encountered several issues with air-cooled chillers over the years. I understand that even the best systems can face problems. It is important to address these issues quickly to maintain system efficiency. Let’s explore the common errors and what causes them. I have seen firsthand how operational and maintenance-related issues can affect performance.
Common errors include insufficient cooling, noisy operation, and short cycling. Maintenance problems such as refrigerant leaks, dirty condenser coils, and compressor failure also occur. Environmental factors like high ambient temperatures and low airflow can further affect performance.
In my experience, operational issues like insufficient cooling are common. These often result from iced-up evaporators or degraded coolants. Sometimes, the condenser coils become dirty, which reduces the efficiency of heat transfer. Noise is another issue; loose parts or worn-out bearings can create vibrations that lead to mechanical failures. I have also seen cases of short cycling where the compressor turns on and off too frequently. These problems are sometimes linked to incorrect refrigerant levels or faulty thermostats.
Maintenance-related errors are equally important. For example, refrigerant leaks can lower system pressure and increase energy consumption. Regular inspections are crucial to catch these leaks early. Dirty condenser coils also cause trouble. Dust and debris can block airflow and lower the chiller’s effectiveness. I have often advised my clients to schedule regular cleaning. Moreover, compressor failure is a severe issue. This can be due to inadequate lubrication or electrical issues. Keeping up with maintenance can prevent these errors and extend the system’s life.

What are Commercial Chiller Repair and Maintenance Tips?
In my years of service, I have learned that regular repair and maintenance are the backbones of a reliable chiller system. I have seen many systems perform better with proper care. Commercial chillers require constant attention to avoid costly downtime. Let’s talk about practical tips that I have used and recommended to my clients.
Regular inspections, cleaning of filters and coils, and prompt repairs are essential. Lubrication, electrical checks, and refrigerant management play critical roles in keeping chillers running efficiently. Professional maintenance programs are highly recommended.
I always advise my clients to carry out daily visual inspections. Checking for debris, leaks, and unusual sounds can catch problems early. It is also important to inspect evaporator and condenser coils regularly. I recommend cleaning or replacing air and water filters as needed. Keeping moving parts well-lubricated is vital. Electrical checks should not be ignored either. Loose connections or unbalanced voltages can cause significant issues.
Another tip I often share is refrigerant management. Monitoring refrigerant levels and checking for leaks can prevent many problems. I also recommend that you engage licensed HVAC technicians for complex repairs. Professional assistance can prevent voiding warranties and ensure high-quality repairs. Lastly, adopting a preventive maintenance schedule helps. I usually suggest daily, weekly, quarterly, and annual checks. Keeping detailed records of all maintenance activities is a good practice. For further information, you might want to visit Wikipedia on HVAC.
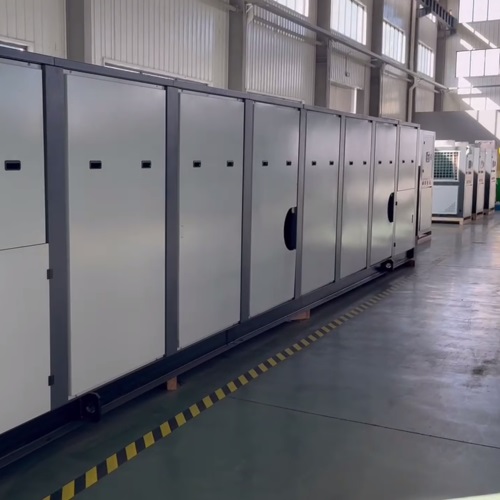
How Can Chiller Systems Be Retrofitted for Better Performance?
I have often faced questions on how to make older chiller systems more efficient. Many companies can save energy and improve performance through retrofitting. I have seen first-hand that even minor upgrades can yield big results. Let’s discuss some practical retrofitting strategies that I have used with success.
Retrofitting measures include installing variable-speed drives on compressors and fans, upgrading to advanced control systems, and modernizing refrigerants. These changes can reduce energy consumption and boost efficiency. Regular maintenance and load balancing also contribute to improved performance.
Retrofitting is an effective way to improve chiller efficiency without replacing the entire system. One key strategy is to install variable-speed drives (VSDs) on compressors and fans. VSDs adjust motor speeds based on real-time cooling demands. I have observed energy savings of 20–40% during partial load conditions with this upgrade. Another approach is to upgrade control systems. Modern controls can dynamically adjust chilled water supply temperatures and manage load balancing effectively. This simple change can boost efficiency by several percentage points.
In addition, modernizing the refrigerant is important. I have seen systems perform better when updated to low-GWP refrigerants such as R-513A. This change not only complies with environmental regulations but also enhances performance. Upgrading compressors to more efficient models, such as magnetic-bearing or variable-speed types, is another effective measure. Moreover, integrating energy management systems (EMS) can provide real-time monitoring. This allows you to adjust operating parameters quickly and maintain optimal performance. For more details on energy management, you might visit Wikipedia on Energy Management.
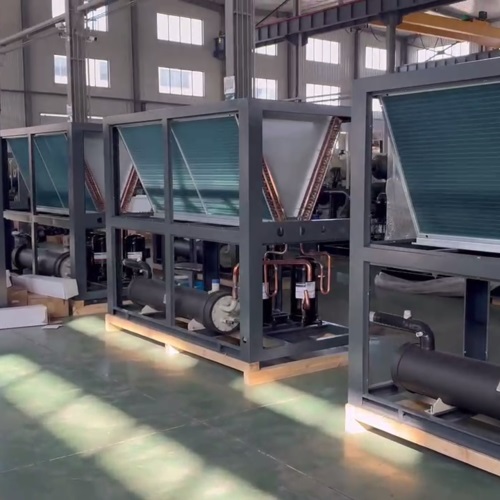
Conclusion
I hope that this article has provided you with a clear and valuable insight into air-cooled chillers. I have shared my personal experiences and detailed technical knowledge to help you understand these systems better. We explored the fundamental principles of how they work, common errors, repair and maintenance tips, and retrofitting strategies for enhanced performance.
By understanding the basics and knowing how to address common issues, you can make informed decisions for your cooling systems. I always believe that a well-maintained chiller not only improves efficiency but also extends the life of your investment. Moreover, regular maintenance and smart retrofitting can lead to significant energy savings and better overall performance.
I invite you to use the external links provided for further reading. Reliable sources such as Wikipedia on Chillers offer neutral and detailed background information. As someone with over 20 years of experience, I understand the challenges you face and I am here to share insights that truly matter. Let us work together to ensure that your cooling systems are as efficient and reliable as possible.
Thank you for taking the time to read this article. I look forward to sharing more insights with you in the future. If you have any questions or need further advice on industrial cooling solutions, please feel free to reach out. We are all in this journey together, and I am committed to helping you achieve the best performance from your chiller systems.