Have you ever wondered whether your facility needs a heat exchanger or a chiller? You’re not alone! Many industry professionals face confusion over these two critical components. I’ve spent over 20 years in the industrial refrigeration and heat exchange field, and today I’ll share clear insights that will help you make an informed decision.
Heat exchangers transfer heat between two fluids without mixing them, while chillers use refrigeration cycles to actively cool fluids. Choosing the right equipment can significantly enhance your facility’s efficiency and performance.
Understanding the core differences, applications, and benefits of each system is crucial. In this comprehensive guide, we’ll delve deeper into how heat exchangers and chillers function, explore their different types, and determine the scenarios in which each is best utilized.
What Are Heat Exchangers and Chillers?
You might be familiar with the terms “heat exchanger” and “chiller,” but what exactly distinguishes one from the other?
A heat exchanger is a device that transfers heat from one fluid to another without mixing them. A chiller, on the other hand, is an active cooling system that removes heat using refrigeration cycles.
Heat exchangers rely on tubes or plates to efficiently transfer heat between two separate fluids. This mechanism is ideal for maintaining temperatures and improving energy efficiency in various industries. Chillers are more complex, equipped with components like compressors, condensers, evaporators, and expansion valves, actively reducing fluid temperature and providing precise cooling solutions.
Here’s a quick comparison table for clarity:
Feature | Heat Exchanger | Chiller |
---|---|---|
Components | Tubes, plates, fins | Compressor, evaporator, condenser, expansion valve |
Operating Principle | Passive heat transfer | Active refrigeration cycle |
Temperature Range | Wide | Lower, typically 41°F to 5°F |
Complexity & Cost | Simpler, lower cost | Complex, higher investment |
Before diving deeper, let’s explore the specific types and their practical applications.
Types of Chillers
Choosing the right chiller type is crucial for efficient cooling operations. Here’s what you need to know:
The three basic types of chillers are Vapor Compression, Vapor Absorption, and Air/Water-Cooled Chillers.
Vapor Compression Chillers
These chillers are the most commonly used type, utilizing an electric compressor to circulate refrigerant through the system. They’re further divided into air-cooled and water-cooled variants, suitable for diverse operational needs.
Vapor Absorption Chillers
Instead of electric compressors, these chillers use heat sources (like steam, hot water, or solar heat) to drive the refrigeration cycle. They are energy-efficient and ideal for large facilities with available heat sources.
Air-Cooled vs Water-Cooled Chillers
Air-cooled chillers are compact and easier to maintain since they eliminate the need for cooling towers. Water-cooled chillers offer greater efficiency, stable operation, and a longer lifespan but require additional infrastructure and water treatment.

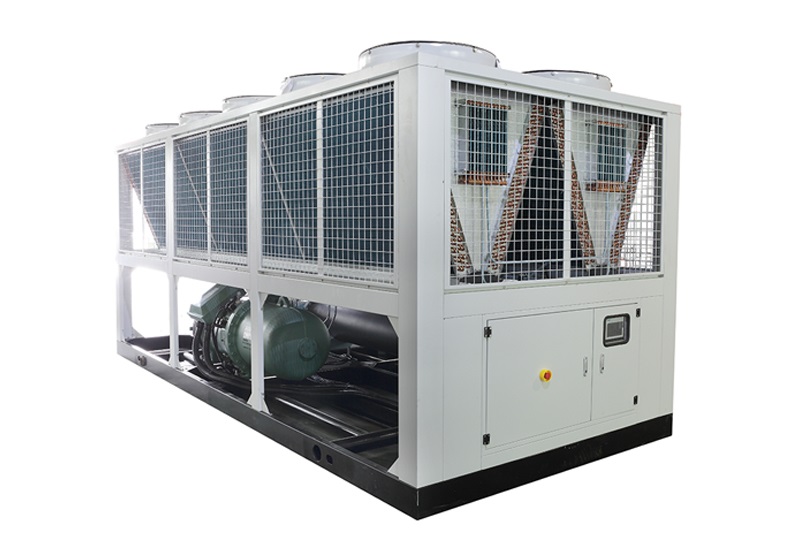
Types of Heat Exchangers
Understanding heat exchanger types ensures optimal heat transfer efficiency tailored to your specific needs.
The three primary types of heat exchangers are Shell-and-Tube, Plate, and Finned-Tube Heat Exchangers.
Shell-and-Tube Heat Exchangers
Known for reliability and versatility, these heat exchangers have tubes within a cylindrical shell, ideal for handling large temperature and pressure differences common in industries like petrochemicals and power generation.
Plate Heat Exchangers
These are compact, offering high heat transfer efficiency by stacking thin plates. They are especially suitable for food processing, refrigeration, and HVAC applications due to their space-saving design.
Finned-Tube Heat Exchangers
With fins attached externally to tubes, they significantly enhance heat exchange capabilities. Commonly used in HVAC systems and industrial processes requiring efficient heat dissipation.
Let’s now determine when and why you should choose one system over the other.
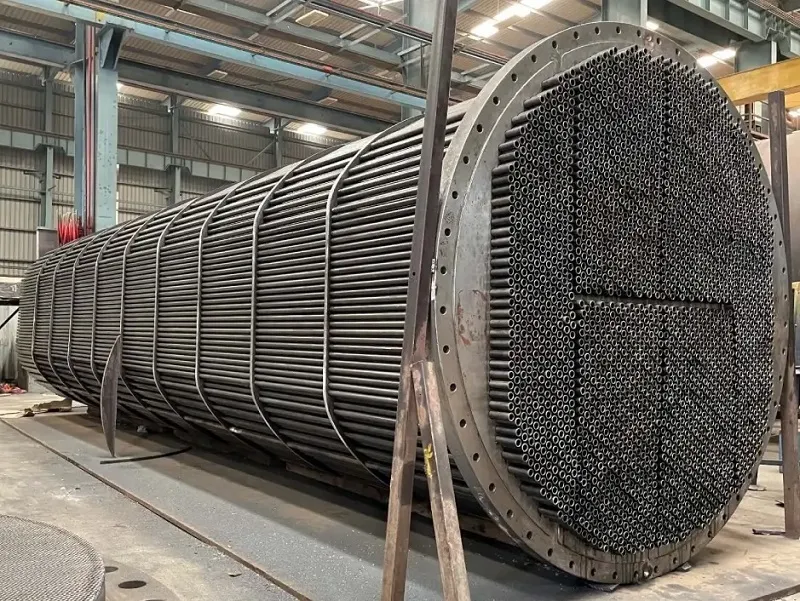
When Should You Use Heat Exchangers vs Chillers?
The decision between using a heat exchanger or a chiller depends largely on your specific operational requirements.
Use heat exchangers for general heat transfer tasks, temperature regulation, or improving efficiency. Choose chillers when active and precise cooling is necessary.
Heat Exchangers Applications:
- HVAC systems: To regulate indoor air temperature.
- Food and Beverage Industry: For controlled heating or cooling during processing.
- Chemical and Petrochemical industries: For managing extreme temperatures and corrosive materials.
- Pharmaceutical applications: Essential for maintaining consistent thermal conditions.
For authoritative external resources, consider checking Wikipedia on heat exchangers.
Chillers Applications:
- Commercial HVAC: Large facilities such as hotels, hospitals, and universities.
- Industrial production: Preventing equipment overheating in industries like plastics, automotive, and pharmaceuticals.
- Data centers: Keeping sensitive electronic equipment cool.
- Medical Facilities: Ensuring precision cooling for medical equipment and patient safety.
Explore more about chillers from Wikipedia on chillers.
Conclusion
Choosing between heat exchangers and chillers doesn’t need to be complicated. Understanding their functionalities, types, and ideal scenarios will ensure your equipment choices align with your operational goals, saving energy, costs, and enhancing overall productivity.
If you’re still unsure about which system fits your needs best, our team at IceStar Energy Technology Co., Ltd is always here to help. With over two decades of experience, we can offer customized industrial refrigeration and heat exchange solutions designed specifically for your applications.
Contact us today for personalized advice!