In today’s competitive industrial and commercial HVAC landscape, selecting the right chiller system is a decision that impacts not only energy consumption and operational efficiency but also long-term return on investment. While names like Trane, York, Carrier, and Daikin have long dominated the global market, emerging high-performance brands like IceStar are challenging the status quo by delivering equal or superior performance at a more accessible price point.
This article provides a comprehensive, data-driven comparison between IceStar and the world’s top chiller manufacturers. If you’re considering your next investment in an air-cooled or water-cooled chiller system, read on to discover why IceStar may be the smart alternative.
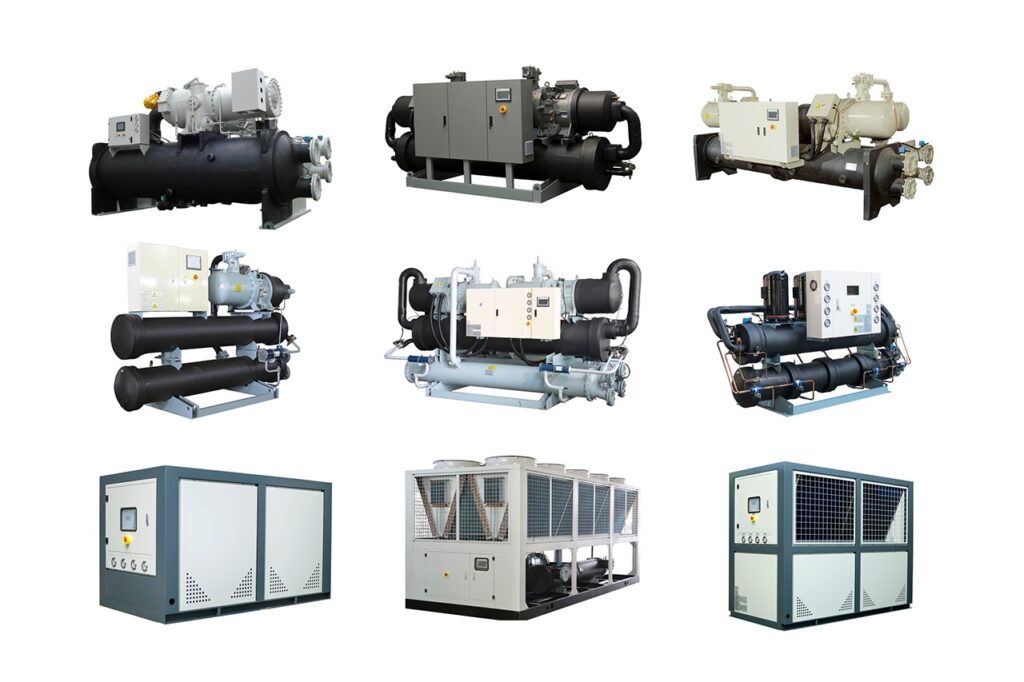
Energy Efficiency & Performance
Top Brands (Trane, York, Carrier, Daikin) are renowned for their high energy efficiency, often featuring advanced variable speed drives, magnetic bearing compressors, and proprietary energy optimization software. However, these advantages often come with a significant premium.
IceStar, leveraging cutting-edge engineering and R&D, offers:
- High COP (Coefficient of Performance) comparable to leading brands
- Proprietary high-efficiency heat exchangers and optimized refrigerant cycles
- Availability of both fixed-speed and inverter-driven models
➡️ Result: For many industrial applications, IceStar’s systems deliver up to 15% lower energy consumption under similar load conditions while maintaining reliability.
Customization and Flexibility
Top Brands often offer standardized systems designed for mass deployment, especially in commercial real estate and data centers. While these systems are well-engineered, they may lack flexibility when it comes to specialized industrial needs.
IceStar excels in offering tailored solutions:
- Custom-built capacities from 10 to 1000+ tons
- Adaptable temperature ranges (from -25°C to +35°C)
- Special corrosion-resistant materials for chemical, marine, or high-humidity environments
- Compact designs for space-constrained installations
➡️ Result: IceStar provides greater adaptability for complex or unique operational requirements across industries like pharmaceuticals, plastics, metallurgy, and food processing.
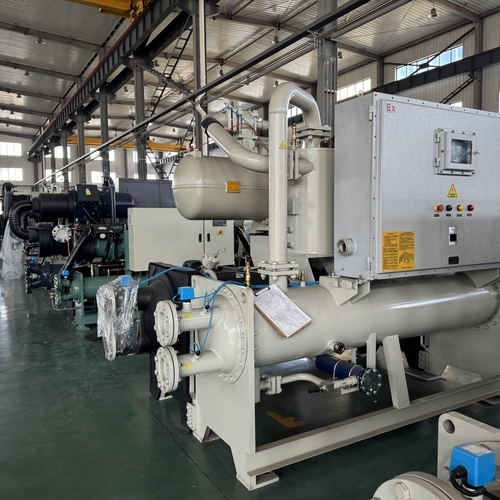
Cost-Effectiveness
Initial procurement cost is a critical factor for many project managers and procurement officers.
Top Brands often require:
- Premium pricing structures
- Expensive after-sales service contracts
- Longer lead times that can affect project schedules
IceStar provides:
- Transparent and competitive pricing
- Lower total cost of ownership (TCO)
- Free technical support during installation and commissioning
- Quicker lead times (typically 20–30 days)
➡️ Result: Customers save 20–40% in upfront costs and benefit from faster project execution, while enjoying comparable system lifespan and performance.
Technological Innovation
Top Brands have vast R&D budgets and have pioneered many of the features now standard in modern chillers. That said, newer brands are catching up quickly.
IceStar incorporates advanced technologies such as:
- Touchscreen PLC controllers with real-time diagnostics
- IoT-enabled remote monitoring platforms
- Integration-ready with Building Management Systems (BMS)
- Eco-friendly refrigerants (R134a, R513A, R410A options)
➡️ Result: IceStar bridges the innovation gap with a modern, user-friendly, and smart control ecosystem designed for future scalability.
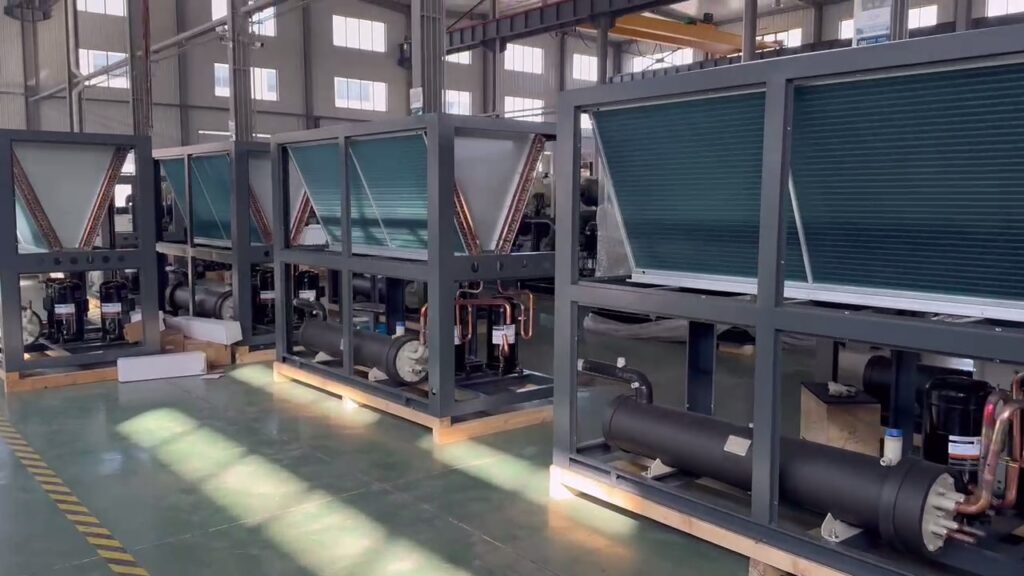
Reliability and After-Sales Service
Buyers often worry that lesser-known brands might compromise on quality or lack global support. While this can be true in some cases, IceStar prioritizes reliability as a core brand value.
Key IceStar service features:
- Rigorous testing protocols: Every chiller is factory tested before shipping
- Full documentation and remote commissioning support
- Rapid-response technical support teams (on-site or online)
- Global spare parts logistics network
➡️ Result: IceStar delivers exceptional uptime and peace of mind, with service responsiveness that often exceeds expectations.
Certifications and Compliance
Global projects require adherence to a wide range of safety, energy, and environmental standards.
IceStar systems are certified to meet:
- CE, ISO9001, RoHS, and relevant industry-specific standards
- Optional compliance with UL, ASME, and AHRI where needed
- Customized documentation support for smooth customs clearance and project tenders
➡️ Result: Clients benefit from hassle-free procurement and qualification for international projects.
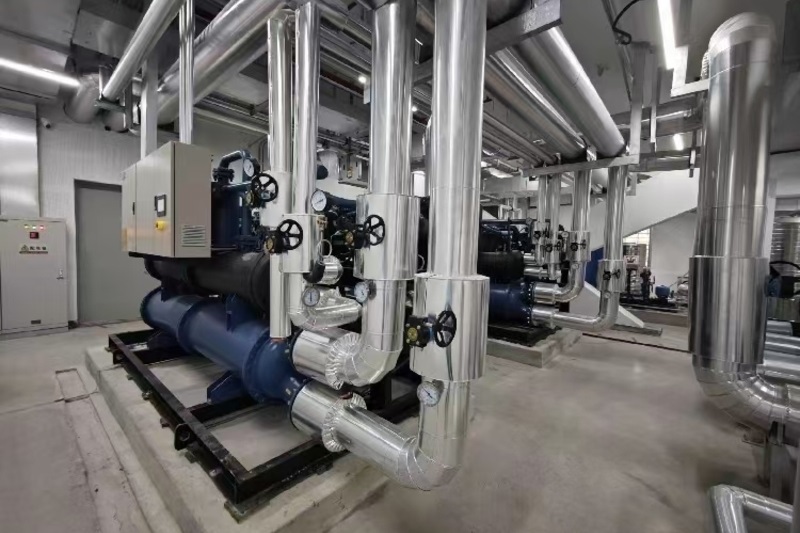
Global Reach with Localized Support
Though IceStar is a newer player on the global stage, it has quickly built a presence across key markets including Southeast Asia, the Middle East, South America, and Africa.
Through a combination of:
- Strategic partnerships with local agents
- Regional technical training and service hubs
- Multilingual customer support
➡️ Result: IceStar ensures that buyers receive the same level of service and support as with traditional Tier-1 brands.
A Value-Driven Alternative
While top-tier brands like Trane, Carrier, and York offer strong reputations and proven track records, they may not always align with the modern buyer’s priorities: flexibility, speed, innovation, and value.
IceStar fills this gap by offering:
- Comparable performance
- Greater customization
- Lower lifecycle costs
- Strong global support
In a world that demands both efficiency and agility, IceStar is not just a budget-friendly option — it is a strategic choice.
Ready to explore how IceStar can support your project?
Contact us today for a free consultation and performance estimate tailored to your application.